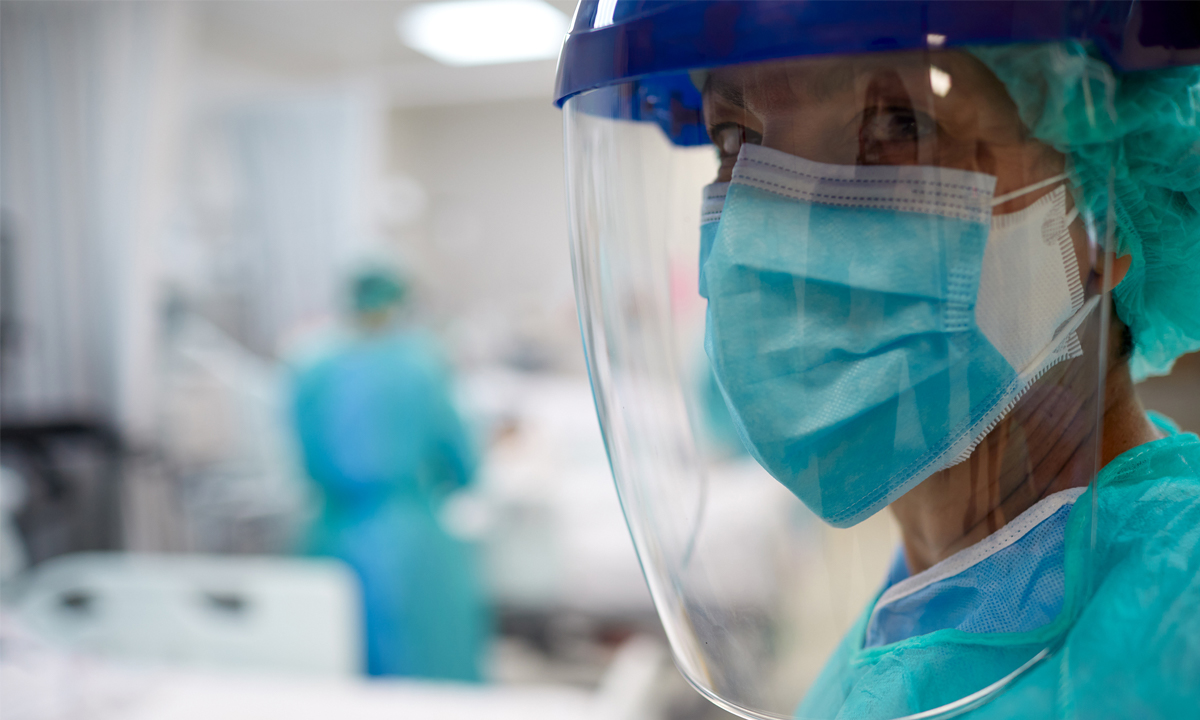
Have you adopted a lean mindset and culture as part of your organization’s overall journey for continuous improvement? With health care organizations all around the world tasked to find innovative ways to improve quality and value while reining in costs, lean methodology provides a proven approach to achieving high-quality care and value for patients while eliminating waste and redundancy,according to Katherine Santos, MBA, Vice President of Strategy and Operational Excellence at Legacy Lifecare. Santos is also Capstone Director of Harvard Medical School’s certificate program, Leadership in Medicine: Southeast Asia.
The Origins of Lean
Santos explains that lean, otherwise known as the Toyota Production System, originated in the automotive industry in the mid-20th century and pulled together concepts aimed at improving efficiency and increasing value for the customer. Over the past two decades, these concepts associated with lean have increasingly been adapted by high-performing health care organizations in the United States to combat rising costs while improving patient outcomes. By applying lean to existing systems, organizations have achieved significant improvements in patient safety and quality such as reducing medical errors, increasing patient satisfaction, and improving access to care, all while also reducing costs.
Yet the practice of lean has been slower to take off in other parts of the world. This is the reason why Leadership in Medicine: Southeast Asia delves into the fundamentals of implementing lean processes and overcoming roadblocks to guide current and emerging leaders from Malaysia, Southeast Asia, Australia, and the Pacific region. These participants can benefit from increasing their knowledge of lean within the broader context of safety, quality, and organizational management and leadership to help their organizations succeed over the long-term.
What is Lean?
Lean is defined as “the relentless pursuit of the perfect process through waste elimination and respect for people.” To better understand this definition, Santos breaks it down into three main parts:
Relentless pursuit of the perfect process – This refers to lean’s goal of building a culture of continuous improvement;
Waste elimination – This is lean’s secret to maximizing value for the customer and improving efficiency by removing waste from processes such as defects, delays, waiting, extra processing, inventory, and movement.
Respect for people – This is derived from the fundamental belief that frontline employees (i.e. the people who do the work every day) are the experts in the process and are best equipped to identify problems and solutions.
When adopting a lean strategy, Santos says there are some key questions to ask yourself, such as:
- Who are the customers of your system, and what do they value most?
- What pain points or problems prevent your staff from delivering value to your customer?
- What change can you make that will result in an improvement?
- What measures will you track to know that the change is an improvement?
Fundamental Principles of Lean
Though the adoption of lean may vary by organization, there are five core principles that are at the foundation of this methodology. These include:
- Specify value from the perspective of your customer – “In health care, our main customer is the patient,” Santos says. “Lean teaches us that we should learn what our patients value and how their experience could be improved to support the best outcome.” She explains that value to the patient is any activity that improves the patient’s health, well-being, and experience. An example is a patient receiving the right care at the right time in the right place.
- Identify the value stream or patient journey – "When examining the patient journey, it is important to identify the steps of the process that add value to the patient’s care,” Santos says. “By mapping out the current process, health care leaders are able to expose waste.” Typical examples of waste in a value stream include duplicate steps, unnecessary work, and lack of clear roles and responsibilities. Revealing these issues is the first step in determining how these steps can be better organized to deliver the best outcome.
- Make the process and value flow without interruptions – “Health care processes should be aligned to facilitate the smooth flow of patients and information,” Santos shares. This means employing concepts like eliminating waste between steps, adjusting for demand, and avoiding batching and queuing. Setting up highly visible standardized workstations and uniform processes reduce variation so that care is delivered as efficiently as possible.
- Let the customer pull services – “Lean emphasizes that a process should never push a service to a customer who is not ready to receive it because doing so increases delays and ties up capacity,” Santos explains. Every step in the patient journey should pull the necessary people, information, and supplies one at a time only when required. “By better synchronizing the key parts of treatment with patients’ needs, we can minimize the time a patient is in treatment and also ensure the proper allocation of resources when and where they are needed,” she says. This is contrary to the typical view that resource utilization must be maximized, which often results in waste.
- Pursue perfection – “Under lean, processes are meant to be developed and amended continuously in pursuit of the ideal,” Santos emphasizes. The pursuit of perfection is a continuous stream of small improvements generated by staff over time. “In this way, lean can help health care organizations continuously adapt to an ever-evolving environment and patient needs in order to deliver the highest quality care,” she adds.
Putting Lean into Action
To better understand the fundamental principles of lean and its benefits, Santos described a common health care experience, an outpatient visit with a doctor. “In a typical doctor’s visit, the patient defines value as the time spent with the physician receiving a diagnosis and getting treatment,” Santos says. However, when the patient journey or value stream is examined, there are many examples of waste that prevent the visit from being an ideal experience for the patient, physician, and clinic staff. These include delays due to missing or incomplete paperwork, staff searching for supplies because exam rooms are stocked differently and overbooked physician schedules leading to long wait times.
Santos explains that applying lean principles can dramatically improve the experience of not only the patient, but also the physician and clinic staff. To streamline the visit, clinic leaders can make changes like asking the patient to electronically complete paperwork in advance, building a more realistic physician schedule with rules that prevent overbooking, and setting up the exam room supplies in a standardized way. All these improvements using lean result in saving time and resources, shortening patient wait times, improving physician and staff efficiency, and leading to higher satisfaction for patients and providers.
Staff Empowerment and Leadership Support as Critical Success Factors
Santos stresses that implementing lean is not just about using the tools but about embracing a complete shift in culture and mindset. For one, all leaders in a lean organization must create the environment where applying lean thinking can deliver results. This includes giving people time and space to contribute. “All leaders should spend time in the workplace observing and listening to care providers, staff members, and patients,” she says. “By being on the units, they will then see the waste and opportunities for improvement.”
Ultimately, the success of lean is in empowering employees and staff to do and improve work processes. “Lean stresses the concept that employees and staff should be both the doers and the improvers of work,” Santos says. Lean is inclusive and motivational because it encourages a problem-solving culture where everyday problems and frustrations are quickly resolved. Staff will save an enormous amount of time and effort which can then be used more effectively. Because of this, there is a high level of buy-in that allows changes to be sustained over time. “If you eliminate waste and add value in a system, your staff satisfaction will go up since you are taking away steps that waste your employees’ time. You allow them to do what they do best and make it easier for them to do their job,” she says.
Starting Small and Building
“The desired outcome of implementing lean in a health care organization is everyday improvement,” Santos concludes. “The majority of improvements you make using lean methodology may seem small, but they can really add up when everyone is able to find and remove waste from the system by improving their daily work.” The time and resources saved can then be used to provide even more value to the patient.
Leaders who understand the benefits of lean and empower their organizations to apply the principles to continuously adapt and improve are better positioned to lead towards success, no matter what challenges they face. When all of these steps come together, they can be truly transformational.
Written by Lisa D. Ellis